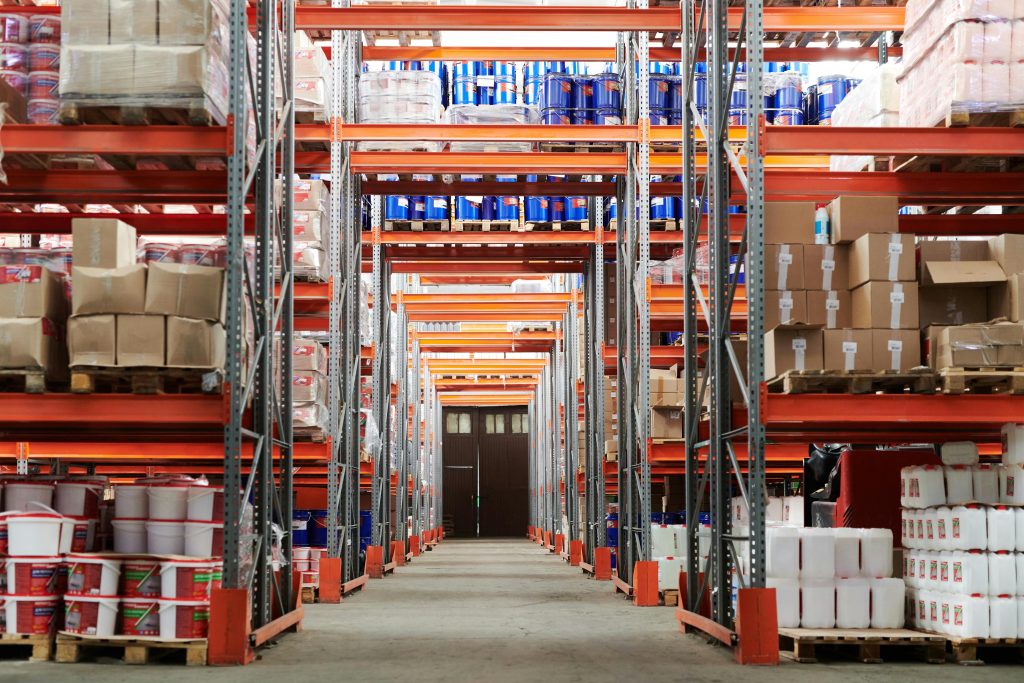
Intralogistyka – czym jest i jak ją optymalizować?
Firmy dążące do zwiększenia swojej efektywności powinny zadbać o optymalizację procesów w obszarze, jakim jest intralogistyka. Odgrywa ona kluczową rolę w wydajnym funkcjonowaniu przedsiębiorstwa –
Nowy wymiar optymalizacji
w przemyśle
Szybka i trwała poprawa wyników
Mocne fundamenty dla dalszego rozwoju
Optymalizacja procesów w firmie produkcyjnej to klucz do wzniesienia jej na wyższy poziom. Wypracowanie efektywnych procesów biznesowych w obszarze logistyki, planowania produkcji oraz optymalizacja procesów produkcyjnych są koniecznymi elementami, o które powinieneś zadbać, aby organizacja szybciej stawiała kolejne kroki naprzód. Jeśli interesuje Cię optymalizacja przedsiębiorstwa oraz rozwój obszarów operacyjnych, to zapraszamy do skorzystania z usług Entra Group.
Jesteśmy doświadczonym zespołem specjalistów, który posiada dwudziestoletnie doświadczenie w obszarze, jakim jest optymalizacja procesów zachodzących w różnego rodzaju firmach. Z naszą pomocą przedsiębiorstwa z wielu branż skutecznie redukują koszty swojej działalności i poprawiają jej efektywność. Współpraca z Entra Group pozwoli na długofalowy rozwój Twojej firmy i zwiększenie jej konkurencyjności. Konkretny plan rozwoju jest niezbędny, aby w przyszłości osiągać założone cele oraz zyskiwać na zmianach zachodzących na rynku.
Skontaktuj się z nami i spraw, aby optymalizacja procesów produkcyjnych i biznesowych w Twojej organizacji stała się faktem.
Oceniamy potencjał poprawy i tworzymy konkretny plan dalszego rozwoju
Redukujemy koszty działalności i dobieramy najskuteczniejszą metodę rozwiązywania każdego problemu
Trwale zmieniamy kulturę organizacji, budujemy kompetencje i zaangażowanie pracowników
Dynamicznie zmieniająca się rzeczywistość rynkowa sprawia,
że na kwestię optymalizacji przemysłu trzeba spojrzeć z nowej perspektywy. Niezbędne stało się połączenie optymalizacji z Przemysłem 4.0, który jest coraz ważniejszym wyznacznikiem rozwoju. Dziś firmy nie tylko muszą działać sprawnie, ale muszą także być przygotowane na niespodziewane sytuacje. Największe szanse rynkowe mają organizacje, które w sposób świadomy i konsekwentny wprowadzają zmiany, dla których rozwój i doskonalenie są codziennością.
Naszą misją jest pomaganie firmom, które nie są w pełni zadowolone z osiąganych wyników. Tym organizacjom, które naprawdę chcą się rozwijać i wierzą w swoją przyszłość. Wspieramy podmioty, dla których optymalizacja procesów biznesowych jest ważna, i które widzą w niej szansę na wzmocnienie swojej pozycji rynkowej. Towarzyszymy firmom, które trwale chcą zmienić kulturę organizacji na proaktywną, otwartą i gotową na nieuchronne zmiany, tak, aby te w większym stopniu stawały się dla firmy szansą, niż problemem.
Optymalizacja procesów w organizacji, zgodnie z tym, co zakłada Model by Entra, dzieli się na cztery fazy:
Jak przebiega optymalizacja procesów przeprowadzana według tych założeń? Na początku współpracy wykonujemy audyt, który umożliwia nam zidentyfikowanie i weryfikację efektywności najważniejszych procesów w firmie. Dzięki zebranym informacjom możemy wskazać obszary, gdzie niezbędna jest optymalizacja procesów. Na podstawie audytu przedstawiamy wnioski, rekomendacje projektów do wdrożenia oraz wskazujemy cele, jakie można za ich pomocą osiągnąć – przedstawiamy Plan Rozwoju prowadzący do skutecznej optymalizacji. Kolejnym krokiem jest wdrożenie nowych procesów oraz maksymalizacja efektywności tych, które już istnieją. W ramach tego etapu prowadzimy szkolenia i warsztaty dla pracowników, którzy potrzebują nowej wiedzy, aby móc odpowiednio dostosować się do wprowadzanych zmian. Nie poprzestajemy na tym i udoskonalamy kolejne procesy w firmie, pracując również nad ich integracją. Poczynione działania sprawiają, że Przemysł 4.0 staje się rzeczywistością we współpracującej z nami organizacji.
Model by Entra jest tworzony przez trzy komplementarne produkty:
Zapoznaj się bliżej z każdym z tych produktów i przekonaj się, jak mogą przyczynić się do rozwoju Twojej organizacji.
Michał Matejczyk
Dyrektor ds. Rozwoju
+48 603 753 779
michal.matejczyk@entra-group.eu
Firmy dążące do zwiększenia swojej efektywności powinny zadbać o optymalizację procesów w obszarze, jakim jest intralogistyka. Odgrywa ona kluczową rolę w wydajnym funkcjonowaniu przedsiębiorstwa –
Firmy korzystają z różnych metod mających na celu zapobieganie występowaniu błędów w realizowanych procesach. Jedną z nich jest Poka Yoke – system bazujący na opracowywaniu
Ważnym zagadnieniem w kontekście prawidłowego funkcjonowania firm produkcyjnych i zadowolenia pracowników są odpowiednio zbudowane systemy premiowe. Zasady premiowania powinny być klarowne i usystematyzowane, a sam mechanizm
Razem przejdźmy ten dystans